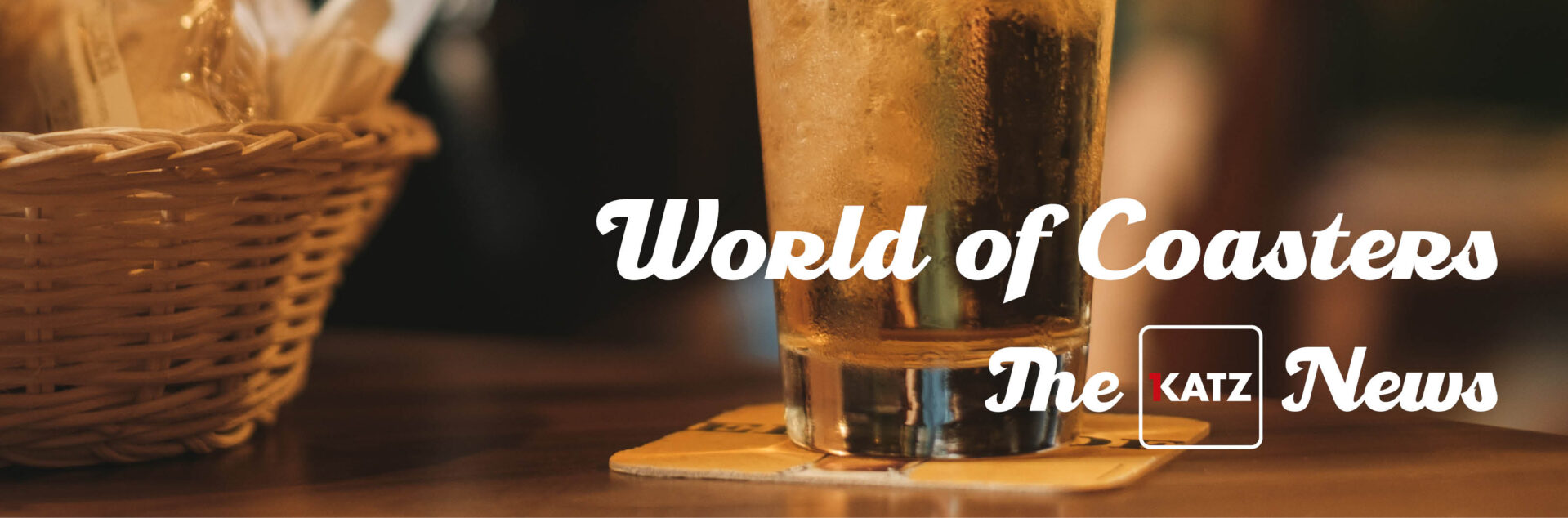
Newsletter #5 | An interview with Katrin Schmidt
“The quality of the raw materials is the key factor; after all, you can’t spin straw into gold.”
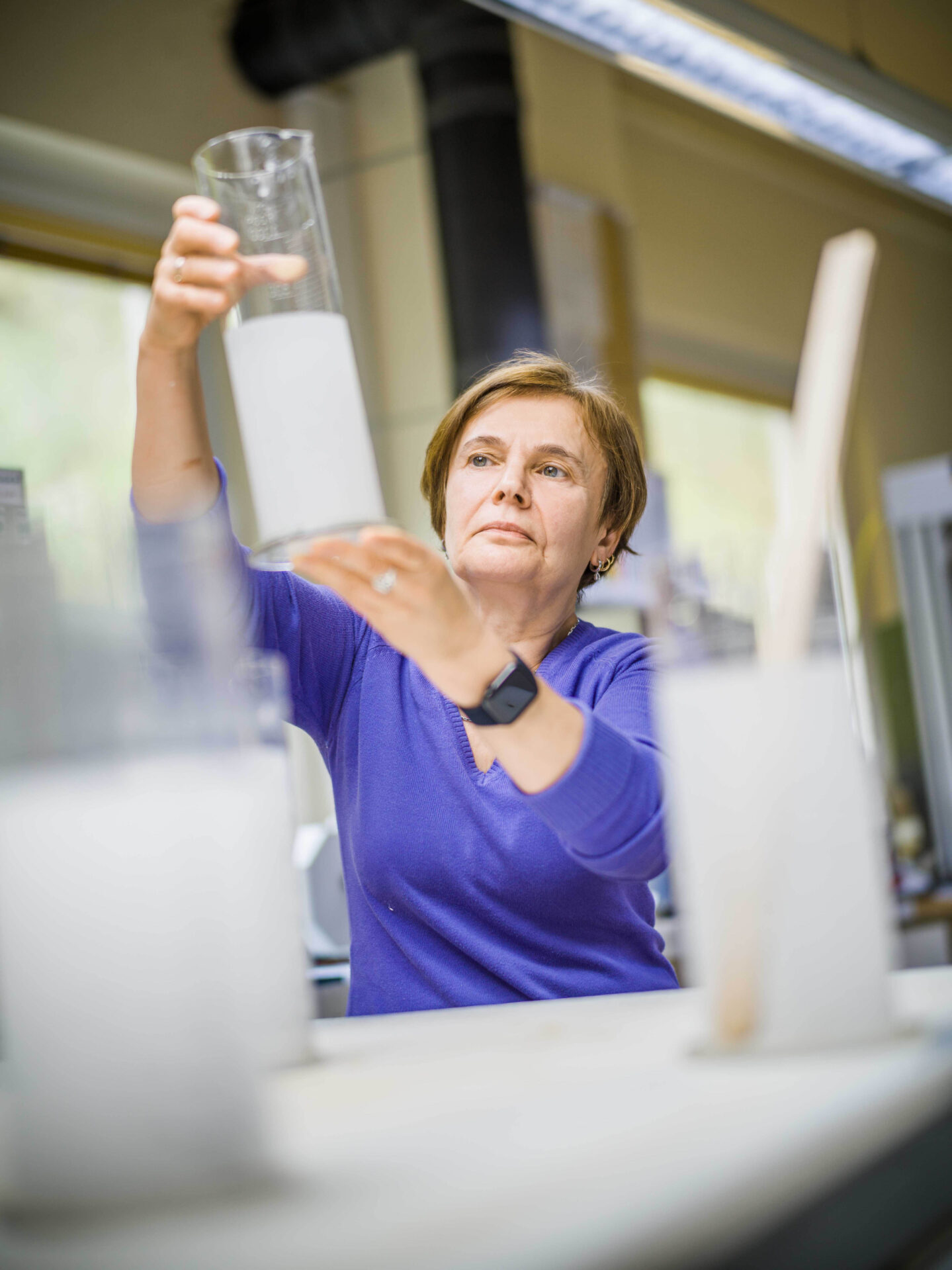
Name: Katrin Schmidt
Job title: Quality Assurance employee
Hobbies: Playing guitar
Age: 61
Joined KATZ in: 2003
Measuring instruments hum quietly away in the background as muffled machine noise floats from the production floor into the adjacent room, and the Murg flows gently by outside the window. The Murg is a small river that runs directly past the KATZ site in Weisenbach on the edge of the Black Forest. Utterly idyllic. The door swings open and a petite figure with short dark hair enters the room. It is Katrin Schmidt, who has called Quality Assurance home for more than 20 years.
How did you end up working at KATZ?
When I was 17, I started an apprenticeship as a chemical lab assistant in a paper mill in East Germany. I stayed there for the next 12 years. However, after the reunification of East and West Germany, the paper mill closed down and my husband started working for a cardboard manufacturer in Gernsbach in 1992. Six years later I joined him and started working for an automotive supplier. While I was there, I trained as a quality assessor and assistant in the Quality Assurance department. By chance, I found out through an acquaintance that KATZ had a vacancy in their QA department, and I saw it as a chance to get back to my roots. And now I am ending my career where it all started: in a paper mill.
What does your role at KATZ entail?
In the Quality Assurance department at KATZ, we primarily work in two areas: the wet area and the dry area. I am mainly responsible for the wet area. This includes checking all raw materials and material suspensions, basically everything that is used to produce the wood pulp board. We also perform regular checks to ensure that our products work properly and run tests on them.
What steps do you take to ensure the quality of the products?
The quality management system and certification in accordance with ISO 9001 form the basis of a continual improvement process and determine which checks need to be performed. It is also essential to check the testing equipment regularly to ensure it is functional.
When purchasing raw materials, we pay close attention to their origin and quality. Then it’s my job to check the materials when we receive them. I collect samples and examine the materials closely. I always say that you need to get the basics right: you can’t spin straw into gold. If I discover any deviations during the checks, I let my colleagues at the cardboard machine know so that they can take corrective action.
What are the three most important features of a beverage coaster?
The most important feature of a beverage coaster is without doubt its absorbency. I check this by adding 10 milliliters of water to the coaster and measuring the time it takes to absorb. Our coasters are highly absorbent. But the whiteness of the top layer is also important to ensure the printed image is high quality, and also the split strength to ensure good stability. Every aspect of our coasters needs to be up to scratch.
What kind of significance do beverage coasters hold for you as an individual?
It makes me proud whenever I come across KATZ products in my day-to-day life. In restaurants, the quality assessor in me often comes out, and I have to inspect the material of the coasters to check if it’s one of ours.