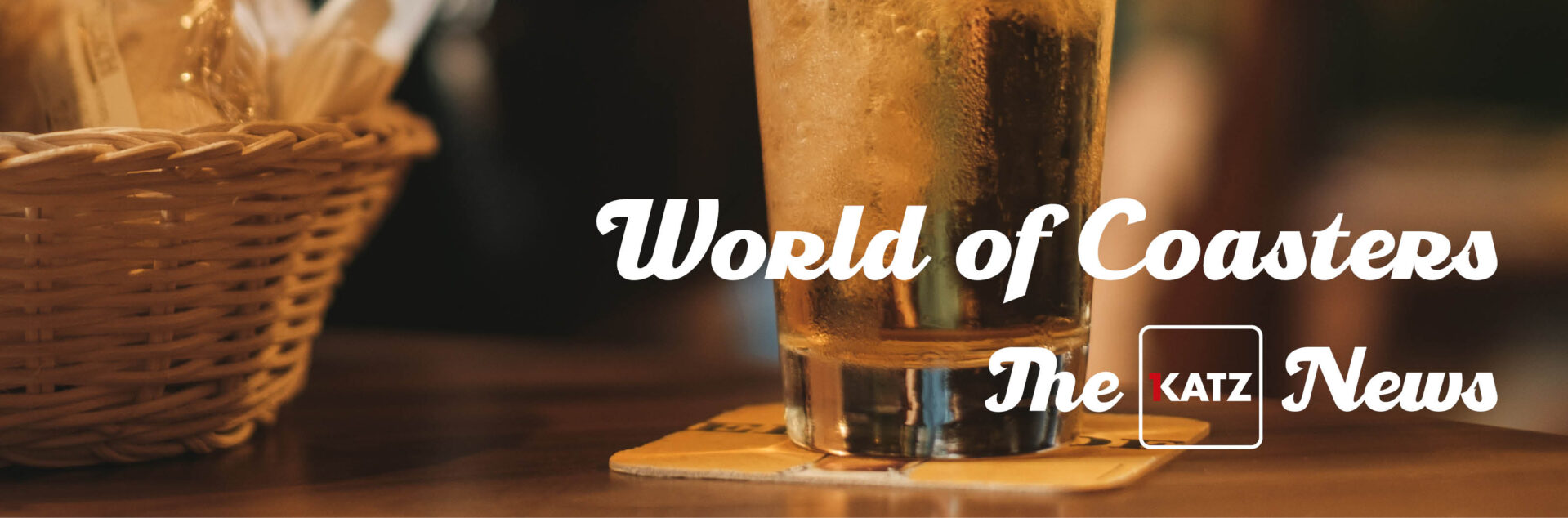
Newsletter #6 | An interview with Timo Heckmann
“Our move to Willstätt gave us enormous latitude when it came to our production operations”
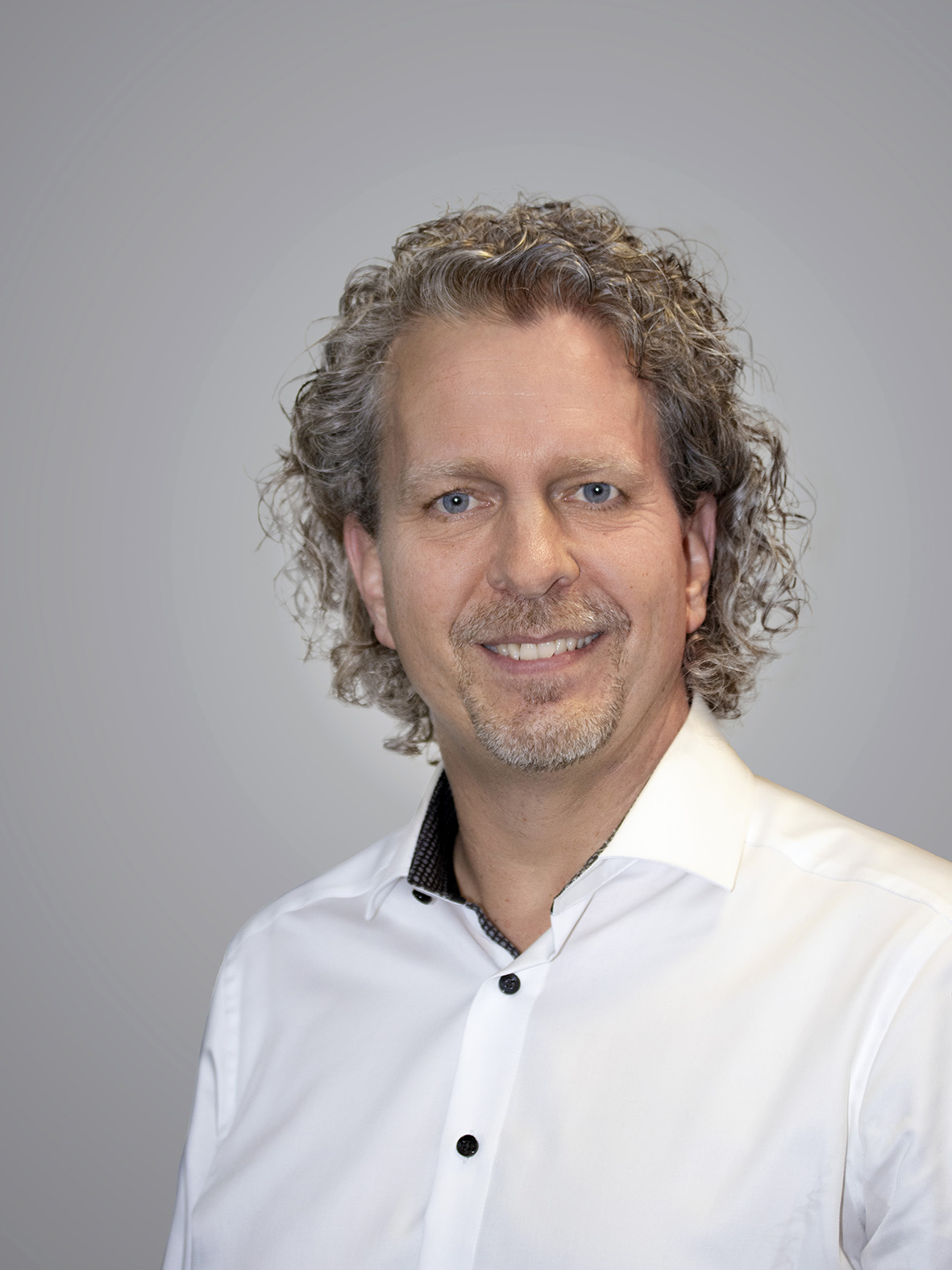
Name: Timo Heckmann
Job title: Print Shop Production Manager
Hobbies: Soccer, traveling to warm countries
Age: 40
Joined KATZ in: 2001
Open the heavy door to the production floor in Willstätt, and you’ll be welcomed by a world where energy abounds: The die-cutting machine’s rhythmic operation fills the air. The printing press keeps at it unremittingly with utmost precision. At the other end of the production line, beverage coasters can be seen in stacks of 100 and then in packs of 1000 before they are placed on a pallet so that they can be taken to the customer in a truck. The faint smell of fresh ink and cardboard permeates the air – a mix that makes it clear right away: Something tangible is being made. And that something is the aforementioned beverage coasters, which will soon tell stories and bring brands to people’s eyes. A powerful scene, not to mention the one where we’re meeting the person in charge of these production operations: Timo Heckmann.
How did you end up working at KATZ?
I started my offset printing apprenticeship at KATZ back in September 2001, when I was only 16. I always liked working with my hands, so I really wanted… well, I’m repeating myself, but to do hands-on work, something in the technical realm. Offset printing just seemed like a natural fit for me.
I’ve been a production manager at KATZ since 2018, and I’ve actually had a pretty exciting career here: Once I was done with my apprenticeship, I worked on the printing press as a machine operator for several years. Then, in 2014, I got the chance to become deputy production manager. Almost needless to say, I also took advantage of a bunch of advanced training opportunities while working at KATZ. For instance, in 2015, I decided to pursue the necessary training to become an industrial supervisor specializing in print media. And obviously you never run out of things to learn as a production manager either, so in 2021 I completed my technical business administration studies.
What does your role at KATZ entail? What do you like best about your work?
My main job is to manage the entire “Print Shop and Processing department”. And to tell you the truth, the work is not just exciting and varied, but also has me be constantly in touch with everyone here. So yes, I obviously have a series of responsibilities regarding our products, but I also get the chance to work more with people who are part of my team. Encouraging and supporting them while shaping my department and processes in a targeted and constructive manner is something that I find incredibly fun. That, together with our machinery, enables us to deliver incredible product results day after day.
Has there been any particular experience or project that really left an impression on you during your time here at KATZ?
Actually, yes, our last big project: Relocating the Print Shop and Processing department to Willstätt. Not only did that involve a new location, but also new machinery. However, those conditions simultaneously gave us tons of latitude to set up things as we saw fit and help shape the site according to our needs.
How would you describe our production operations in Willstätt?
Production in Willstätt is particularly characterized by the fact that everything we put together was novel, innovative, and cutting-edge. All of it was custom-tailored to our beverage coaster production operations, and it truly was a one-time opportunity. To put it simply, we’ve created a production line that has enabled us to maximize the efficiency of our typical workday. Also, I’d be remiss not to mention the fully automatic logistics, which are really something.
How do you make sure that quality always remains consistently high?
We have an inline color measurement system in our printing press that lets us check the quality of print results in enormous detail and keep it at a very high level at all times.
What kind of role does sustainability play in your department?
Sustainability is important everywhere, and we’re certainly no exception. Even if our product is made out of natural materials 100%, we still need to incorporate sustainability into our processing operations. When printing, we make sure to use inks with the least amount of mineral oil possible. In addition, the film we use to pack our beverage coasters is as thin as possible.
We produce virtually zero waste during our operations. In fact, when fleshing out our processes and production sequences, we made sure to really focus on circular economy approaches, and that means that we don’t throw anything away. For example, we press offcuts from sheets into bales and then send them back to our board production teams in Weisenbach so that these bales can be fed into the pulper as raw material. In addition, we have installed an extraction system that sucks up the dust produced by the die-cutter and press it into small briquettes that are also used as raw material for board production. In other words, we’ve made sure that not even dust goes wasted.
What kinds of trends are you seeing in the industry when it comes to printing on beverage coasters?
Beverage coasters are seen as ad space nowadays; not “just” as beermats. Obviously, this means that the print quality on coasters is now subject to more demanding requirements. Printed images are getting increasingly sophisticated, not to mention that they are being changed more often or used for the purpose of special campaigns. All in all, this means that print runs are smaller now, but that’s offset by the fact that we’re getting more frequent orders as a result.